Advantages of Ultrasonic Riveting
What is a Rivet?
Riveting is a fastening method that joins two or more components (typically metal or plastic) using rivets or riveting tools. The process relies on the plastic deformation or mechanical interlocking of the rivet to create a permanent mechanical bond.
Common riveting techniques include thermal riveting, vibration riveting, ultrasonic riveting, laser riveting, and spin riveting. Each method has unique strengths, allowing manufacturers to choose the best process for their needs.
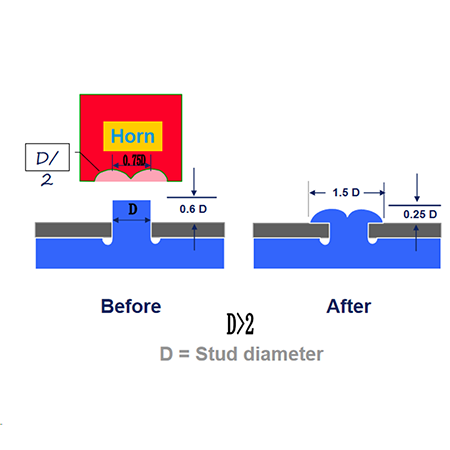
Ultrasonic Riveting
Ultrasonic riveting uses high-frequency vibrations to locally melt plastic components. Under pressure from the welding head, the molten plastic flows into grooves in the metal part, forming a secure rivet joint upon cooling.
Key advantages of ultrasonic riveting include speed, precision, and no consumables. Applications include:
Automotive: Dashboard assemblies, interior trim, and plastic-to-metal fastening.
Electronics: Securing connectors, sensors, and plastic housing components.
Medical: Precision bonding for catheters, filters, and device housings.
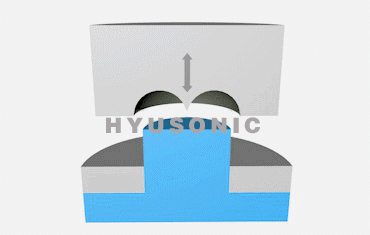
What is the difference between a rivet and a welded connection?
Material Compatibility: Riveting bonds plastics with different melting points and joins plastic to metal, while welding typically only works with similar-melting plastics.
Strength: Rivets create robust physical connections that withstand higher tensile and shear forces, whereas welding may weaken materials.
Aesthetics: Riveted joints often look cleaner, especially with ultrasonic riveting, which allows seamless integration with product designs.
Ultrasonic Riveting Methods
Standard Design: Simple and versatile for most thermoplastics.
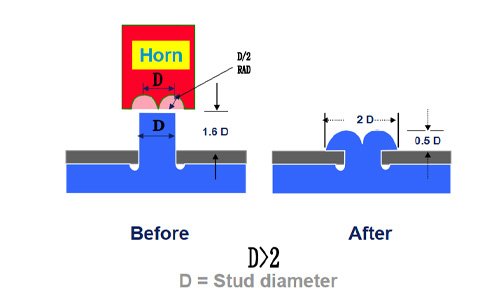
Semi-Circular Design: Smooth, rounded finishes resist wear and shear forces, ideal for appearance-critical products.
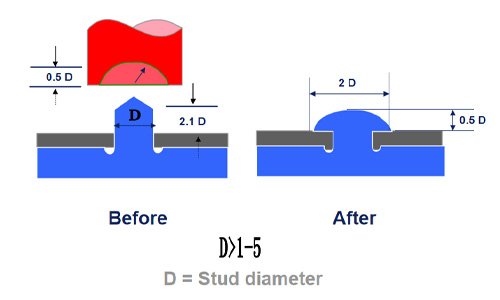
Hollow Design: Lightweight with space savings, maintaining strength for precision components.
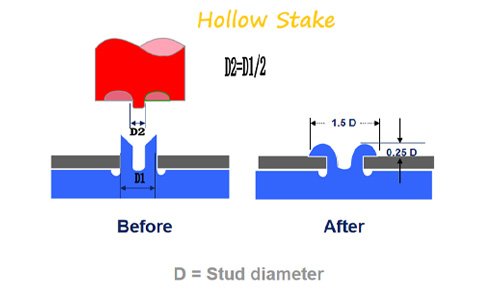
High-Pressure Design: Enhances bond strength and sealing for demanding applications like automotive engine parts.
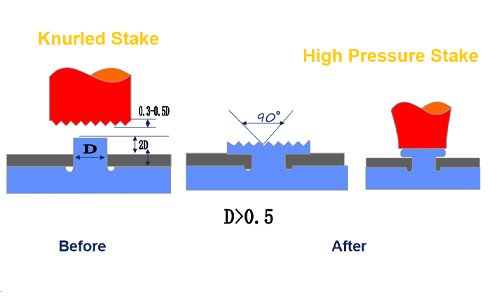
Conclusion
Ultrasonic riveting outperforms traditional methods with higher precision, efficiency, and minimal part damage. Its clean, fume-free process makes it ideal for medical devices and automotive components requiring strict hygiene and durability standards.