Ultrasonic Welding Horns (Sonotrodes)
Precision-machined ultrasonic horns in titanium, Steel, or aluminum for optimal energy transmission. Custom designs for complex geometries (e.g., multi-point welding) with ±0.01mm tolerance. Features include:
✔ Hardened tips for glass-filled materials
✔ FDA-compliant finishes for medical applications
✔ 3D simulation-optimized resonance profiles
Hyusonic ultrasonic sonotrodes are custom-engineered with CAD designs to create optimal structures for diverse welding applications. Prior to manufacturing, each sonotrode undergoes rigorous stress analysis to ensure peak welding performance. We achieve accuracy in horn production using precision CNC machining and laser measurement technology. Our ultrasonic sonotrodes are versatile tools suitable for a wide range of ultrasonic processes, including ultrasonic plastic welding, ultrasonic metal welding, and ultrasonic cutting.
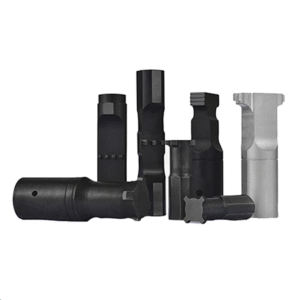
Industry-Proven Designs
Textile/fiber welding horns with serrated tips
Multi-point contact horns for automotive parts
Micro-welding tips for electronic components
Precision Engineering
CNC-machined to ±0.01mm tolerance
Resonant frequency matched to your transducer (15kHz/20kHz/28kHz/30kHz/35kHz/40kHz)
Professional Stress Analysis of Welding Horns for Uniform Amplitude Distribution
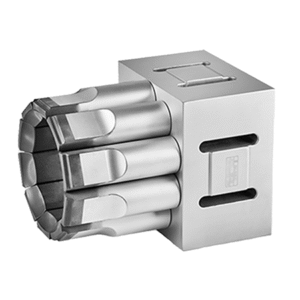
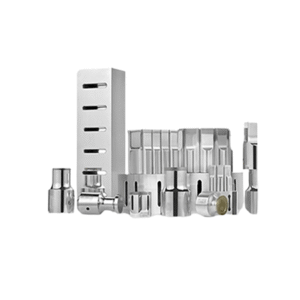
Material Science Expertise
Aircraft-grade titanium (Ti-6Al-4V) for high-amplitude applications
Hardened aluminum alloys for cost-sensitive projects
Custom steel alloys for specialized metal welding
Surface Treatment of Ultrasonic Sonotrode
Due to the high-intensity operation, ultrasonic welding horns are prone to wear, adhesion, corrosion, etc., which lead to performance degradation. Surface treatment can ensure the smooth and uniform surface of the welding horn, avoiding issues such as insufficient welding strength, workpiece deformation, or unsightly weld spots caused by surface defects.
Different surface treatment processes
- Plating process: Commonly, chrome or nickel is plated via electroplating or chemical methods, which can enhance the wear resistance and corrosion resistance of the welding horn, and improve the contact effect between the surface and workpieces.
- Coating process: Common ones include diamond-like carbon (DLC) coating, titanium nitride (TiN) coating, and polytetrafluoroethylene (PTFE) coating, which can significantly extend the service life of the welding horn and reduce material adhesion.
- Polishing treatment: Mechanical or electrolytic polishing reduces surface roughness (Ra≤0.2μm) to minimize material adhesion.
Application Of Ultrasonic Sonotrode
Ultrasonic welding horns can be used for plastic welding, metal welding, non-woven fabric welding, etc. In addition, they can also be applied to the cutting, embossing, riveting, punching, etc. of composite materials such as textile materials, rubber, and leather.
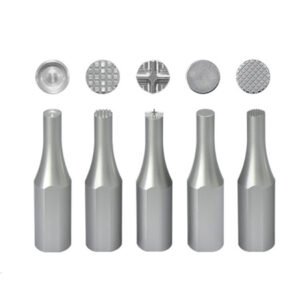
ultrasonic horn design guidelines
Our ultrasonic welding horns require personalized welding solutions to be evaluated based on specific product characteristics, followed by customized processing through mold opening. Only by designing the most suitable welding horns can the optimal welding effect be achieved.
- 1. Contact us to send your product drawings
- 2. Select Material & Frequency
- 3. Receive 24hour Quotation
ultrasonic horn design
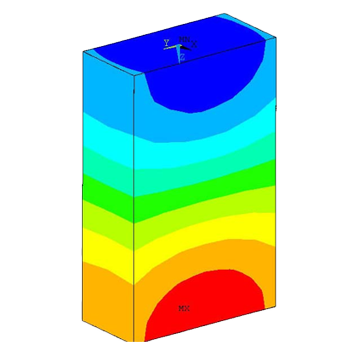
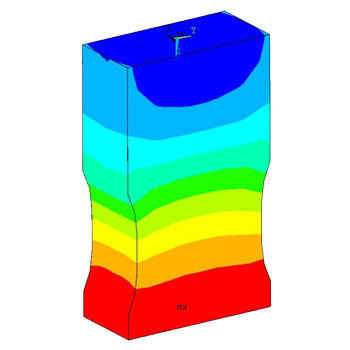
Customer FAQs
What is an ultrasonic welding horn used for?
An ultrasonic welding horn (sonotrode) is a critical component in ultrasonic welding systems that transfers high-frequency vibrations to the workpiece, enabling precise bonding of plastics, metals, or textiles.
How to choose the right ultrasonic horn for plastic welding?
Select based on:
✔ Frequency (15kHz, 20kHz, 28kHz, 30kHz, 35kHz or 40kHz)
✔ Material (titanium for durability, aluminum for cost-efficiency)
✔ Amplitude requirements (25μm–150μm)
✔ Part geometry (flat, knurled, or contoured tips)
What materials are ultrasonic welding horns made of?
Common materials:
Titanium (Ti-6Al-4V) – High strength, long lifespan
Aluminum 7075 – Lightweight, economical
Tool steel – For specialized metal welding
Why does my ultrasonic horn crack or wear out?
Causes include:
✖ Resonance mismatch (incorrect frequency tuning)
✖ Overheating (poor cooling or excessive amplitude)
✖ Material fatigue (low-grade titanium or aluminum)
Can ultrasonic horns be custom-designed?
Yes! Custom horns are CNC-machined to match:
Unique part shapes (e.g., medical device components)
Specific amplitude requirements
Machine compatibility (Branson, Herrmann, etc.)
Where to buy high-quality ultrasonic horns?
Look for manufacturers offering:
✅ ISO 9001 certification
✅ Free CAD design support
✅ Frequency testing reports