What is a Sonotrode in Ultrasonic Welding?
Ultrasonic Sonotrode: Also Known as the Ultrasonic Horn in Ultrasonic Welding Machines
The ultrasonic sonotrode, commonly referred to as the ultrasonic horn, plays a crucial role in the ultrasonic welding process. As a key component of the ultrasonic welding machine, the primary function of the sonotrode is to conduct ultrasonic waves emitted by the ultrasonic transducer. These high-frequency vibrations, generated by the sonotrode, are essential for welding products together. By converting the electrical energy into mechanical vibrations, the ultrasonic sonotrode ensures precise and efficient bonding of materials, especially in applications requiring high-precision welding.
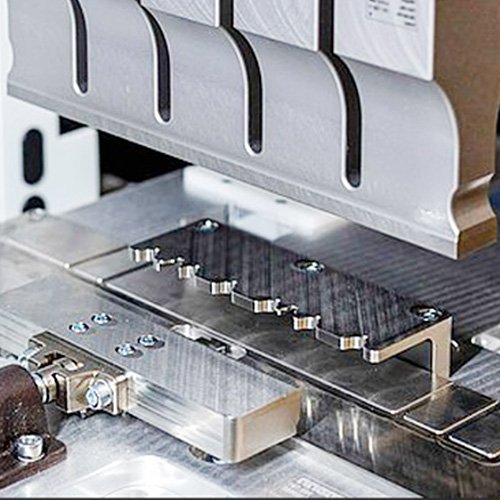
What material is ultrasonic sonotrode made from?
Ultrasonic Plastic Welding Horn Materials
- Beryllium Copper: High thermal/electrical conductivity, for heat dissipation.
- Carbon Fiber Composites: Ultra-lightweight, for special frequency needs.
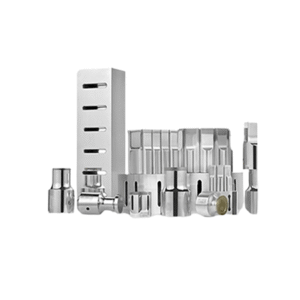
Ultrasonic Metal Welding Horn Materials
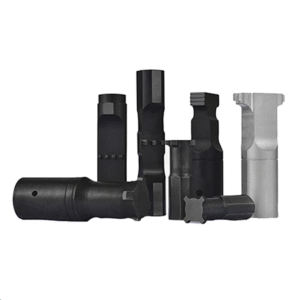
- Molybdenum Alloys: High melting point, for high-temperature welding.
- Nickel-Based Alloys: Superior corrosion resistance, specialized in chemical equipment welding.
Advantages in different applications
The sonotrode is a key component in ultrasonic welding, transmitting ultrasonic energy to achieve precise welding. Its material, design, and precision significantly influence its performance across industries.
In the automotive industry, sonotrode is used for welding plastic parts like headlights and dashboards. Its materials, such as titanium or aluminum alloys, offer high vibration resistance, heat tolerance, and durability. The precise design ensures energy is focused on the weld area, preventing damage to surrounding components.
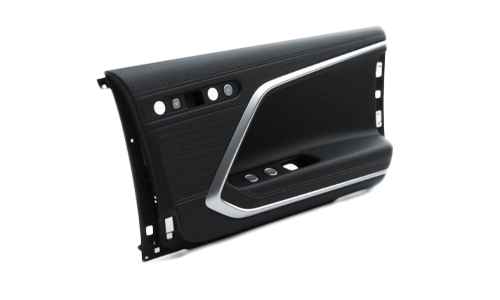
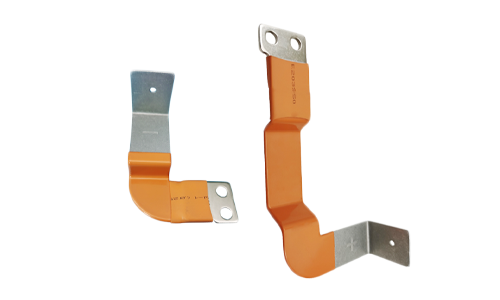
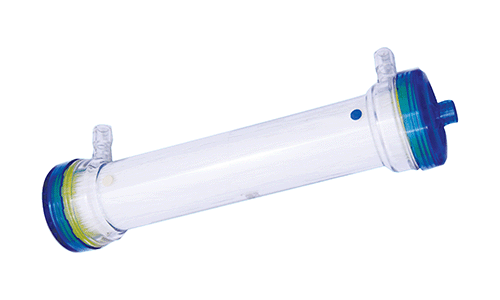
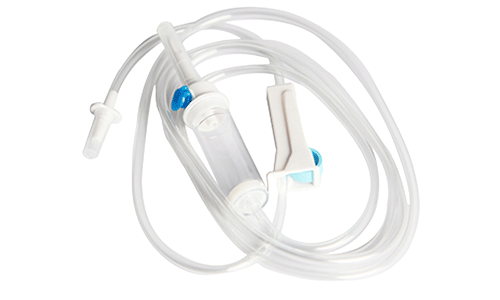
In the medical industry, sonotrode is essential for welding small, sensitive plastic parts in devices like syringes and IV bags. The titanium alloy material ensures cleanliness and prevents contamination, while the precise design ensures strong, clean welds without affecting product integrity.
In the electronics industry, sonotrode is used for welding plastic enclosures and electronic components. Its materials provide excellent vibration conductivity and heat resistance, while the design focuses energy on the weld site, preventing damage to sensitive electronics like circuit boards and displays.

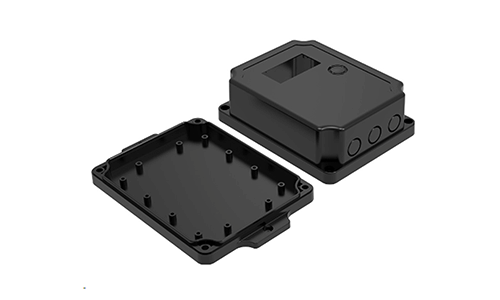
Overall, the sonotrode‘s material selection, design, and precision guarantee high-quality, stable welding in the automotive, medical, and electronics sectors.
How to design ultrasonic sonotrode?
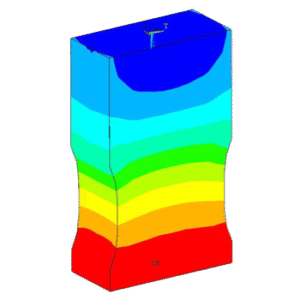
When designing an ultrasonic horn, we need to first consider the ultrasonic frequency. The length of the horn is approximately equal to the half-wave height of the generated wave.The shape of the sonotrode is determined by the product. The welding position and welding horn’s shape should be reasonably designed according to the product material and specific conditions.
Each welding horn needs to be simulated and analyzed for stress, amplitude, and frequency to ensure normal use.
Durability of ultrasonic welding sonotrodes
The service life of the ultrasonic welding horn is related to its material and usage habits.
- Material: Generally, steel welding horns have the strongest hardness and the best metal fatigue properties, while aluminum welding sonotrodes have the weakest hardness and the worst fatigue properties.
- Usage habits: Before using the ultrasonic welding machine, we need to adjust the mold. When installing the ultrasonic horn, you need to ensure that the welding head is firm. We should avoid using hard metal to hit the sonotrode vigorously and damage the ultrasonic sonotrode’s surface.
If the welding frequency and number of times accumulate to a certain level, it will also affect the fatigue of the welding sonotrode and cause damage to the welding horn.
How to judge whether the ultrasonic sonotrode is damaged?
We can judge whether the ultrasonic welding head is damaged by appearance and sound.
- Appearance: Determine the condition of the welding horn by checking whether there are cracks on the welding horn surface(Especially the grooves and screws).
- Sound: If you hear a whistling sound when the ultrasonic welding machine emits ultrasonic waves, you need to check whether the surface of the welding horn is damaged.