What Are Piezoelectric Ceramics for Ultrasonic?
Piezoelectric ceramics are a class of smart materials that exhibit the piezoelectric effect: generating an electric charge when subjected to mechanical stress (direct piezoelectric effect) and undergoing mechanical deformation when exposed to an electric field (inverse piezoelectric effect). These properties make them indispensable in ultrasonic transducers, which convert electrical energy into ultrasonic waves and vice versa. This article explores the history, principles, functions, and applications of piezoelectric ceramics, with a particular focus on their pivotal role in ultrasonic welding technology.
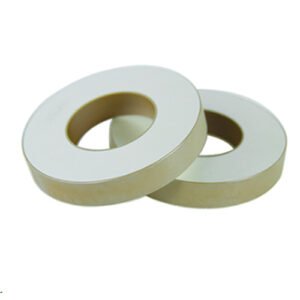
Historical Development
Working Principle
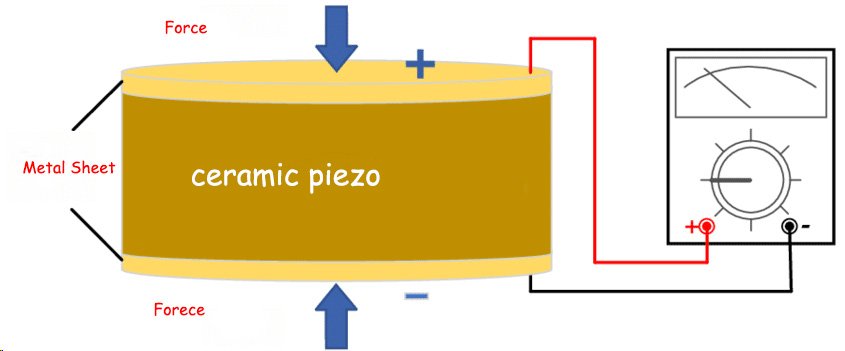
Key Functions in Ultrasonic Transducers
- Generating Ultrasonic Waves: When an alternating electric current (AC signal) is applied to the ceramic element, it vibrates at the same frequency as the current, producing ultrasonic waves. These waves are used in applications like ultrasonic cleaning, welding, and medical imaging.
- Receiving Ultrasonic Signals: In reverse, when ultrasonic waves strike the ceramic element, they generate a small electric signal. This function is crucial in applications such as ultrasonic testing (NDT) and sonar systems, where echoes are detected and analyzed.
- Frequency Tuning: The resonant frequency of the ceramic element determines the operating frequency of the transducer. By adjusting the dimensions and composition of the ceramic, manufacturers can tailor transducers for specific applications, from low-frequency welding (20-40 kHz) to high-frequency medical imaging (2-20 MHz).
Applications
Piezoelectric ceramics play a vital role in numerous industries, with ultrasonic welding being a particularly significant application:
Industrial Manufacturing & Welding Applications
- Plastic Welding: Ultrasonic welding technology driven by piezoelectric ceramics is widely used in automotive components, electronic device casings, and medical devices. It enables fast, clean joining of plastics without adhesives or solvents. Examples include seamless welding of automotive interior parts and precision bonding of smartphone speaker components.
- Metal Welding: In battery manufacturing and electronic packaging, high-frequency ultrasonic welding achieves cold bonding of metals like copper and aluminum, avoiding material oxidation or thermal damage caused by traditional welding methods. Applications include welding lithium-ion battery tabs and precision metal connections on circuit boards.
- Composite Material Welding: For complex structures like multi-layer plastic films and fiber-reinforced composites, ultrasonic welding ensures uniform and robust bonding through precise control of vibration frequency and pressure. This is widely applied in packaging, textiles, and aerospace industries.
Other Application Areas
- Medical Field: Ultrasonic imaging devices utilize the bidirectional conversion properties of piezoelectric ceramics for non-invasive internal organ detection. High-intensity focused ultrasound (HIFU) technology is used for tumor treatment and kidney stone fragmentation.
- Consumer Electronics: The autofocus function in smartphone cameras, ultrasonic fingerprint recognition technology, and the efficient cleaning capabilities of ultrasonic cleaners all rely on precise control of piezoelectric ceramics.
- Non-Destructive Testing (NDT): In aerospace and pipeline inspection, piezoelectric ceramic transducers detect internal defects in materials to ensure structural safety.
Conclusion
Piezoelectric ceramics are the cornerstone of ultrasonic transducer technology, playing a crucial role in modern industrial and technological advancements. Particularly in ultrasonic welding, their efficient energy conversion, precise frequency control, and environmentally friendly processing methods make them ideal for joining plastics, metals, and composite materials. As materials science advances, the development and application of new lead-free piezoelectric ceramics will further drive ultrasonic welding technology toward greater precision, efficiency, and sustainability, bringing breakthrough innovations to industries such as automotive manufacturing, electronic packaging, and medical device production.