Automotive
Ultrasonic welding is ideally suited for automotive interior and functional components such as instrument panels, taillights, safety buckles, and camera housings. Compared to traditional methods like adhesive bonding or infrared welding, ultrasonic welding delivers superior speed and precision while achieving waterproof/dustproof seals with flash-free edges. This technology significantly boosts production efficiency and reduces overall costs.
Hyusonic has collaborated with numerous leading clients in the automotive industry, covering automotive exterior and interior components, automotive lighting and tailgate parts, engine and filtration system components, as well as automotive battery and power system accessories, etc.
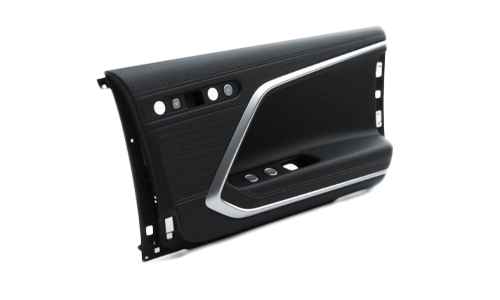



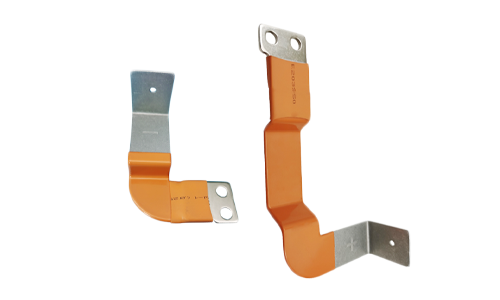

Bumpers
Materials: PP (Polypropylene), ABS (Acrylonitrile Butadiene Styrene)
Advantage: Ultrasonic welding enables rapid splicing of bumpers with brackets and trims, offering high strength (impact resistance ≥ 80% of traditional processes) and a mark-free surface.
Rearview Mirror Housings
Advantage: Excellent sealing prevents water ingress and meets weather resistance requirements.
Dashboard/Center Console
Materials: PC+ABS Alloy, PMMA (Polymethyl Methacrylate, Acrylic)
Advantage: Enables seamless welding of multi-layer structures (e.g., panels and frames), avoids odor from traditional adhesives, and ensures high efficiency.
Door Trim Panels
Materials: PP+EPDM (Ethylene Propylene Diene Monomer), TPE (Thermoplastic Elastomer)
Advantage: Suits bonding soft materials to rigid frames (e.g., sealed welding of door storage slots), with IP54 waterproof rating.
Headlight/Taillight Housings
Materials: PC (Polycarbonate), PPS (Polyphenylene Sulfide, high-temperature resistant)
Advantage: IP67-rated sealing (water and dustproof) withstands 10bar pressure testing, which is ideal for waterproof encapsulation of LED lights to prevent moisture damage.
Filter Housing
Advantages: Good temperature resistance, excellent sealing performance.
Battery Tab Welding
Materials: Copper foil (thickness 5~50μm), aluminum foil (thickness 10~100μm), copper-aluminum composite strip (e.g., T2 copper + 1060 aluminum)
Advantages: Cold welding process (temperature <100℃) without damaging battery active materials; solder joint tensile force ≥80% of the foil’s tensile strength.
contact us for ultrasonic welding solutions
Address
No. 168 Weita Road, Zhangpu Town , Kunshan , Suzhou , Jiangsu , China
Phone/WhatsApp
+(86) 13776317970
rui.zhang@hyusonic.com
hyusonic2009@gmail.com
Why HYUSONIC is Trusted by 5000+ Clients
- Professional Technical Support : 20 years of ultrasonic welding expertise guarantees 100% feasibility assessment for your product's welding needs.
- Thousands of Welding Experiences : With experience serving 5,000+ global clients and welding expertise across 1,000+ product types, we deliver accurate, complete welding solutions for your specific needs.
- German Technology : Hyusonic originated as a German OEM and has established deep technical cooperation with Germany's leading ultrasonic welding experts. We hold ISO 9001, CE certifications, and multiple patents, ensuring premium quality and innovation.