Ultrasonic Plastic Welder Manufacturer
- 15 Years+ Proven Industry Experience
- Smart Welding Integrity Monitoring (SWIM™)
- Medical-Grade Precision And Proven Weld Consistency
Intelligent Inspection: Event-Driven QC + Automatic Monitoring Alarm
Ultrasonic Plastic Welding Machine
Hyusonic produces different types of ultrasonic plastic welding machines, including desktop ultrasonic welding machines, floor-standing ultrasonic welding machines, handheld ultrasonic spot welders, etc. Our ultrasonic plastic welding machines adopt the same Hyusonic family-style design in terms of appearance and color matching. The main differences lie in the main-board components of the ultrasonic generator, the internal structure of the machines, and the intelligent configuration.
- 12-Month Warranty
- Onsite & Online Debugging Training
- Professional & Timely After-Sales Service
- CE / UL / ISO9001 Certification
Advantages of Hyusonic Ultrasonic Welder For Plastic
- German-imported first-tier quality: Hyusonic ultrasonic plastic welding machines use German-imported key ultrasonic systems and components, equipped with a specially designed hard-connection structure, which significantly reduces energy loss, improves conversion efficiency, and ensures ultra-stable power output and welding quality.
- Intelligent quality control monitoring: It supports functions such as automatic defective product monitoring, real-time display of welding curves on the operation screen, and automatic welding alarms. It can seamlessly integrate with Industry 4.0, precisely control welding accuracy through multi-dimensional triggering, and strictly guarantee welding yield rates and product stability. We have collaborated with multiple medical enterprises to perfectly meet medical-grade welding precision requirements.
- Modular automatic development: Supports customized development of electrical control cabinets and screen interfaces, providing one-stop automated equipment and solutions, covering self-developed automatic loading/unloading, multi-station automatic welding, turntable welding, automatic packaging, and labeling functions.
application of ultrasonic welder for plastic
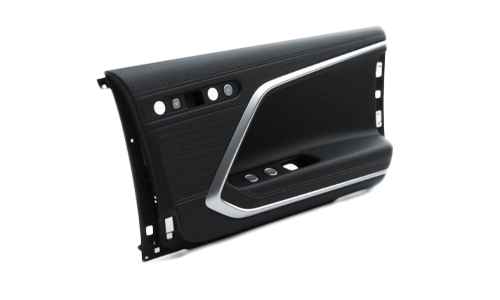
Automotive
Ultrasonic plastic welding can weld automotive interior and exterior trims, sensor housings, battery insulation plates, air filter housings, air filter elements and other parts
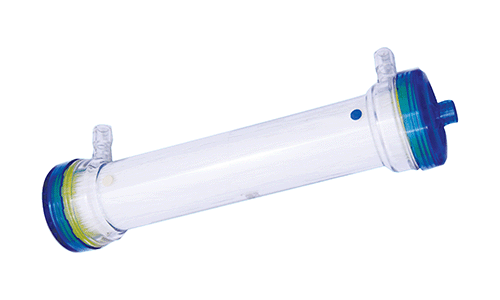
Medical Treatment
Hyusonic ultrasonic plastic welding has a lot of experience in medical welding. It can weld medical test kits, respiratory therapy masks, filter housings, masks, surgical gowns and other medical supplies. Our technology can match the welding requirements of first-line brands and is more cost-effective than other ultrasonic welding machines.

Electronics
Ultrasonic plastic welding can weld most consumer electronic housings, such as headphones, mobile phones, charger housings, game controller housings, etc. It can also weld the operating panels of household appliances and industrial electronic connection housings.
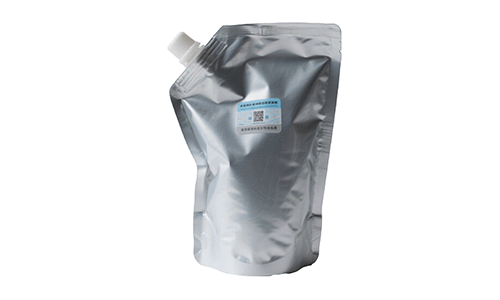
Packaging
Ultrasonic plastic welding can be used for cosmetic tail sealing, plastic daily necessities, plastic films, composite material sealing welding, etc., with the advantages of strong airtightness, strong waterproofness, and cleanliness, eliminating pollution and oxidation of the products caused by welding.
Various ultrasonic welding processes
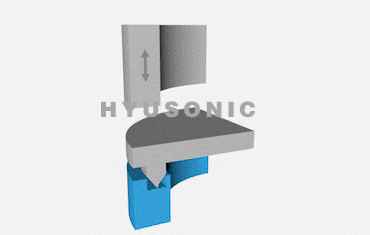
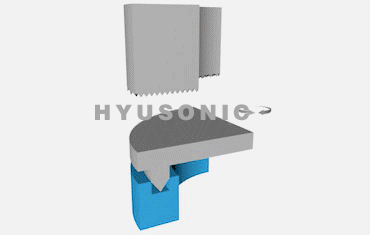
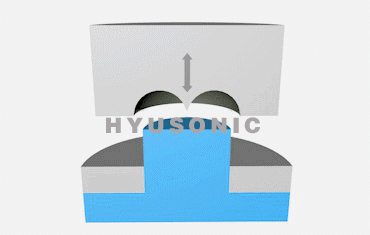
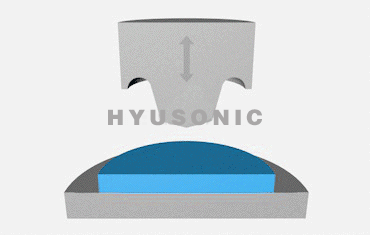
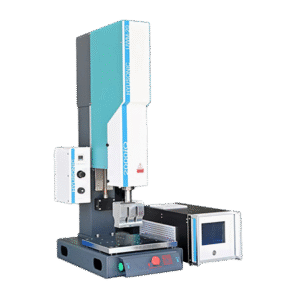
Intelligent Ultrasonic Plastic Welder iQ Series
- European Imported Ultrasonic Components
- Full-Series Modular Design
- CE & ISO 9001 Certified
- 6 Welding Modes & 4 Trigger Modes
- Real-Time Monitoring & Quality Control
Hyusonic has specialized in ultrasonic plastic welding for over 15 years, serving more than 5,000 clients and accumulating experience in welding solutions for over 10,000 products. Our ultrasonic plastic welding machines match the quality of first-tier brands, utilizing European-imported components. They feature functions such as automatic defective product identification, real-time welding curve output, and multi-dimensional precision control. With operating frequencies ranging from 15-40kHz, our machines achieve medical-grade precision and stability, making them widely applicable in industries such as healthcare, automotive, electronics, and packaging.
Your satisfaction is our goal
Professional Ultrasonic Plastic Welder Manufacturer
Customer FAQs
How does ultrasonic plastic welding work?
Ultrasonic welding uses high-frequency vibrations (15-40kHz) to generate friction heat between thermoplastics, melting materials under pressure to form a molecular bond—no adhesives or external heat required. Key components: generator, transducer, and horn.
What plastics can be welded ultrasonically?
- General-purpose thermoplastics: Polyethylene (PE), polypropylene (PP), polystyrene (PS), ABS (Acrylonitrile Butadiene Styrene).
- Engineering plastics: Nylon (PA), polycarbonate (PC), polyoxymethylene (POM), polymethyl methacrylate (PMMA).
- High-performance engineering plastics: Polyphenylene sulfide (PPS), polyether ether ketone (PEEK).
- Filled/modified plastics: Glass fiber (GF)-reinforced plastics (e.g., PA66+30%GF), flame-retardant or conductive plastics (subject to additive compatibility).
What is the cycle time of ultrasonic plastic welding?
Typical cycles range 0.1-3 seconds, depending on material thickness and joint design. Our systems achieve 0.3-second welds for thin-wall applications.
Can ultrasonic welding join dissimilar plastics?
A compatibility chart is available for download only if they share similar melting points (e.g., ABS to PC).
What’s the lifespan of a titanium horn?
Titanium horns last 2-5 years with proper maintenance. Check for cracks or frequency drift annually.
Send your inquire now
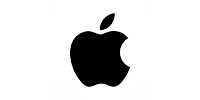
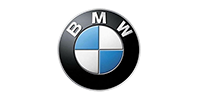

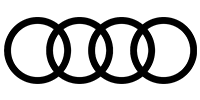
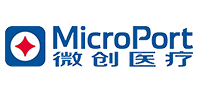

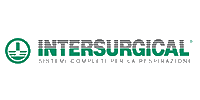

Ultrasonic Welding Plastic Material Compatibility Guide
Material | Weldability | Optimal Frequency | Joint Design | Key Considerations |
---|---|---|---|---|
ABS | Excellent ★★★★★ | 20-30 kHz | Energy Director | Fast cycles, high strength |
Polycarbonate (PC) | Very Good ★★★★☆ | 20 kHz | Shear Joint | Pre-dry (<0.02% moisture) |
PVC (rigid) | Good ★★★☆☆ | 20 kHz | Energy Director | Ventilation required |
Nylon 6 | Fair ★★☆☆☆ | 30-40 kHz | Staking Joint | Must pre-dry (4h @ 80°C) |
Polypropylene (PP) | Poor ★★☆☆☆ | 30 kHz | Chisel Edge | Requires additive-modified grade |
Acrylic (PMMA) | Difficult ★☆☆☆☆ | 15-20 kHz | Near-Field Welding | Low amplitude, brittle |
PPS (30% GF) | Difficult ★☆☆☆☆ | – | Mechanical Fastening | Glass fibers block bonding |
Ultrasonic Welding vs Laser Welding vs Hot Plate Welding: Technology Comparison
Criteria | Ultrasonic Welding | Laser Welding | Hot Plate Welding |
---|---|---|---|
Principle | High-frequency vibration creates friction heat | Laser beam locally melts materials | Direct contact with heated plate |
Speed | ⚡ Fastest (0.1-3 sec/cycle) | Moderate (2-10 sec/cycle) | Slowest (5-30 sec/cycle) |
Material Compatibility | Thermoplastics (ABS, PC, PP, Nylon) | Requires transparent+absorbent plastic combinations | Thick thermoplastic parts |
Joint Strength | ★★★★★ (80-100% of base material) | ★★★★☆ (Material-dependent) | ★★★☆☆ (Potential heat weakening) |
Equipment Cost | $$$ (Mid-range) | $$$$$ (Highest) | $$ (Lowest) |
Energy Consumption | Lowest (Localized heating) | High (Laser power demand) | Highest (Continuous plate heating) |
Automation Compatibility | ★★★★★ (High-speed lines) | ★★★☆☆ (Precise alignment needed) | ★★☆☆☆ (Slow cycle) |
Typical Applications | Car light housings, mask ear loops, connectors | Medical tubes, transparent packaging | Automotive fuel tanks, large pipes |
Advantages | No consumables, fastest for small parts | Non-contact, aesthetic seams | Best for very thick parts |
Limitations | Unsuitable for very large/high-glass-fiber parts | Material pairing restrictions | Thermal distortion risk |