ultrasonic metal welder manufacturer
- 15 Years+ Proven Industry Experience
- Smart Welding Integrity Monitoring (SWIM™)
- Fast welding, high strength, clean, and low resistance
Intelligent Inspection: Event-Driven QC + Automatic Monitoring Alarm
Ultrasonic Metal Welding Machine
Hyusonic manufactures ultrasonic metal welders, ultrasonic wire splicers, ultrasonic spot welders, and ultrasonic metal tube sealers. These machines are used for welding copper, aluminum, magnesium, nickel, and other non-ferrous metal wire harnesses, metal foil, soft-pack battery cells, and terminal welding. The entire product line utilizes a modular design, allowing customization as benchtop or desktop models, and even integration into automated systems.
Advantages of Hyusonic Ultrasonic Metal Welding Machine
HYUSONIC’s in-house ultrasonic metal welding machines create solid-state joints for copper, aluminum, and specialty alloys without the need for melting or external heating. They are ideal for electric vehicle (EV) battery, microelectronics, and precision wire harness manufacturing.
- Precise Control: Digital amplitude adjustment control from 10% to 100%. It can simultaneously set multi-dimensional upper and lower limit threshold controls, such as time, energy, and distance to ensure output accuracy.
- Intelligent Control: Up to 6 operation modes and 4 triggering conditions. It supports Industry 4.0, traceability and upload of product welding records, automatic alarm and monitoring of defective products, and real-time viewing of welding curves.
- Stable Quality: Using German imported ultrasonic system and an independently developed operating system, it fully meets high-standard industry requirements, coupled with perfect after-sales service.
Our Value
Direct Factory, More Reliable
As a true manufacturer, we ensure higher quality control, fast response, and professional support. Unlike traders, we offer consistent service from production to after-sales, giving clients a more stable and dependable cooperation experience.
Top Components, Global Support
We use globally trusted parts like Siemens, SMC, and etc. This ensures high machine reliability and makes local replacements easy for international users—saving time and reducing maintenance effort.
Wide Range, Transparent Pricing
From entry-level to high-end models, our ultrasonic welders suit all needs and budgets. Clear classification and pricing let customers select the right configuration with confidence and no hidden costs.
Certified & Patent-Protected Tech
Our machines are CE, ISO-certified and backed by multiple patents. With strong R&D, we deliver safe, innovative, and performance-driven solutions for demanding industries worldwide.
application video
How Does Ultrasonic Metal Welding Work?
Ultrasonic metal welding uses high-frequency vibrations and pressure to create solid-state bonds between metals. The vibrations generate frictional heat at the interface, softening the materials without melting. Pressure then fuses them together. It’s fast, clean, and ideal for joining thin or dissimilar metals.
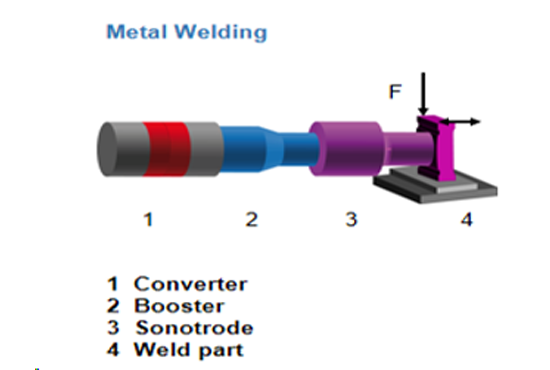
Why Choose Our Ultrasonic Metal Welder?
✔ Oxide-Free Joints – Vibration removes surface oxides, achieving 500+ MPa tensile strength
✔ Energy Efficient – 60% lower power consumption vs laser welding
✔ Material Versatility – Weld dissimilar metals (Cu-Al, Ni-Ti) with <5% resistance increase
✔ Industry 4.0 Ready – PLC controls with Ethernet/IP, MQTT, or OPC UA protocols
Your satisfaction is our goal
Professional Ultrasonic Metal Welder Manufacturer
Key Applications of ultrasonic metal welder
Industry | Typical Welds | Technical Advantage |
---|---|---|
EV Batteries | Tab-to-busbar, Foil stacking | No thermal damage to Li-ion cells |
Electronics | Sensor pins, RFID antenna coils | 0.01mm precision, no flux residue |
Automotive | Wire harness terminations | Vibration-resistant (compliant with LV214 standard) |
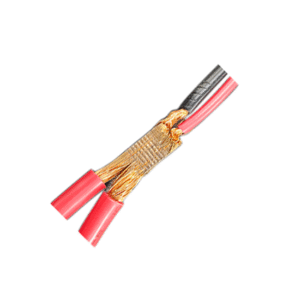
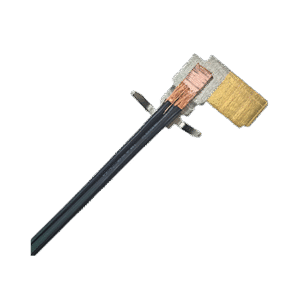
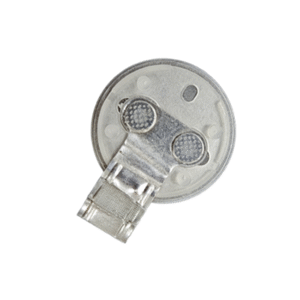
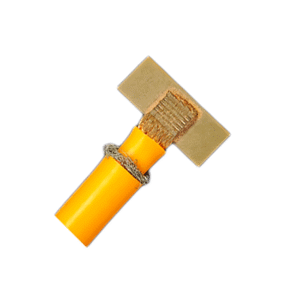
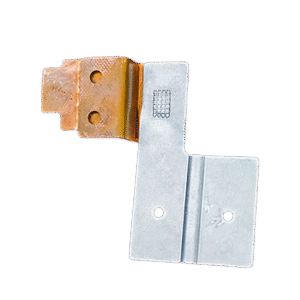
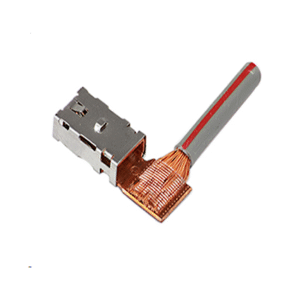
What Our Clients Say
Customer FAQs
How does ultrasonic metal welding work compared to laser welding?
Ultrasonic metal welding uses high-frequency vibrations (20-40kHz) to create solid-state bonds without melting, while laser welding melts materials. Key differences:
✔ No heat distortion – Ideal for battery tabs & sensitive electronics
✔ Lower energy cost – 60% less power than laser
✔ Material flexibility – Bonds dissimilar metals (Cu-Al, Ni-Ti) components: generator, transducer, and horn.
Can you weld copper to aluminum with ultrasonic welding?
Yes! Ultrasonic welding is the preferred method for Cu-Al bonds in EV batteries and wire harnesses. Benefits:
✔ Oxide-free joints – Vibration removes surface oxides
✔ Low resistance – <5% increase vs. 20% with soldering
✔ No filler material – Pure metal-to-metal bonding
Is ultrasonic metal welding suitable for EV battery manufacturing?
Absolutely. Used by Tesla, CATL, and BYD for:
• Tab-to-busbar connections (0.2s/weld, 500+ MPa strength)
• Foil stacking – Up to 0.05mm thin layers
• No thermal damage – Preserves electrolyte integrity
What frequency is best for ultrasonic metal welding?
Depends on material thickness:
• 20kHz – Thick joints (>1mm) like busbars
• 30kHz – Foils (0.01-1mm) for batteries
• 40kHz – Micro-welds (<0.Z1mm) in electronics
How to test the strength of ultrasonic metal welds?
Industry-standard methods:
1️⃣ Peel test – Measures interfacial strength
2️⃣ Cross-section analysis – Checks bond penetration
3️⃣ Resistance measurement – Critical for electrical parts
Send your inquire now
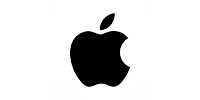
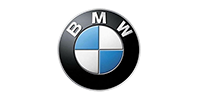

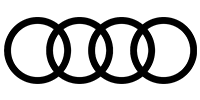
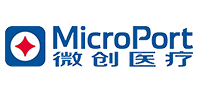

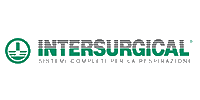
